La forge « à la catalane »
Une forge à la catalane est une usine sidérurgique dans laquelle on produit du fer à partir de ses minerais, en employant des processus technologiques de réduction directe, sans passer par l’étape de production de fonte, comme dans un haut-fourneau. Apparue dans les Pyrénées Ariégeoises au cours du dix-septième siècle, c’est un perfectionnement des procédés utilisés, depuis le treizième siècle, dans les moulines à fer. Les opérations d’obtention du fer durent environ 6 heures et sont conduites selon un processus complexes par des brigades de huit ouvriers.
En termes de métallurgie contemporaine, le minerai de fer est un oxyde de fer que l’on réduit en plusieurs étapes en utilisant du charbon de bois – constitué principalement de carbone. L’agent réducteur est le monoxyde de carbone CO provenant de la combustion incomplète du charbon de bois à une température d’environ 950°C. L’art des forgeurs consiste à maitriser la conduite du bas-fourneau – le creuset – pour obtenir des températures plus élevées (1200°C) tout en favorisant en même temps la production d’oxyde de carbone.
Les forgeurs ariégeois se transmettaient un savoir-faire issu de l’expérience qui leur permettait de mener à bien cette opération de réduction. Le produit brut obtenu au sortir du bas-fourneau, le massé, était ensuite affiné par cinglage sous un marteau pour produire des fers marchands de diverses qualités.
La première description complète de cette méthode fut donnée, en 1838, par l’ingénieur civil Tom Richard qui passa cinq ans à étudier les forges du Pays de Foix et à expérimenter.
En vallée de l’Ouzoum, vers 1663, Louis d’Incamps abandonna l’ancienne forge de Louvie – qui ne fut plus utilsée que comme martinet ou logement – pour construire une forge nouvelle au Hougarou (Nogarot). Il fit reconstruire la forge de Saint-Paul d’Asson. Ces deux forges à la catalane fonctionnèrent jusqu’en 1866. En Béarn, la forge de Béon et celle d’Isale, furent aussi des forges à la catalane.
Ces forges utilisent trois dispositifs complémentaires
• un bas fourneau où on réduit le minerai en présence de charbon de bois, jusqu’à obtention d’une loupe de fer ou massé
• une soufflerie hydraulique d’un type particulier utilisant la trompe des Pyrénées,
• un marteau hydraulique, le mail et son enclume où le massé est cinglé pour éliminer les scories.
L’agencement et la disposition de ces dispositifs varie peu d’une forge à l’autre. Les vestiges des trois forges d’Asson, Nogarot et Béon montrent la même organisation : les trompes à gauche, le bas fourneau au milieu, le marteau à droite dans une halle de 20 m sur 15 m environ.
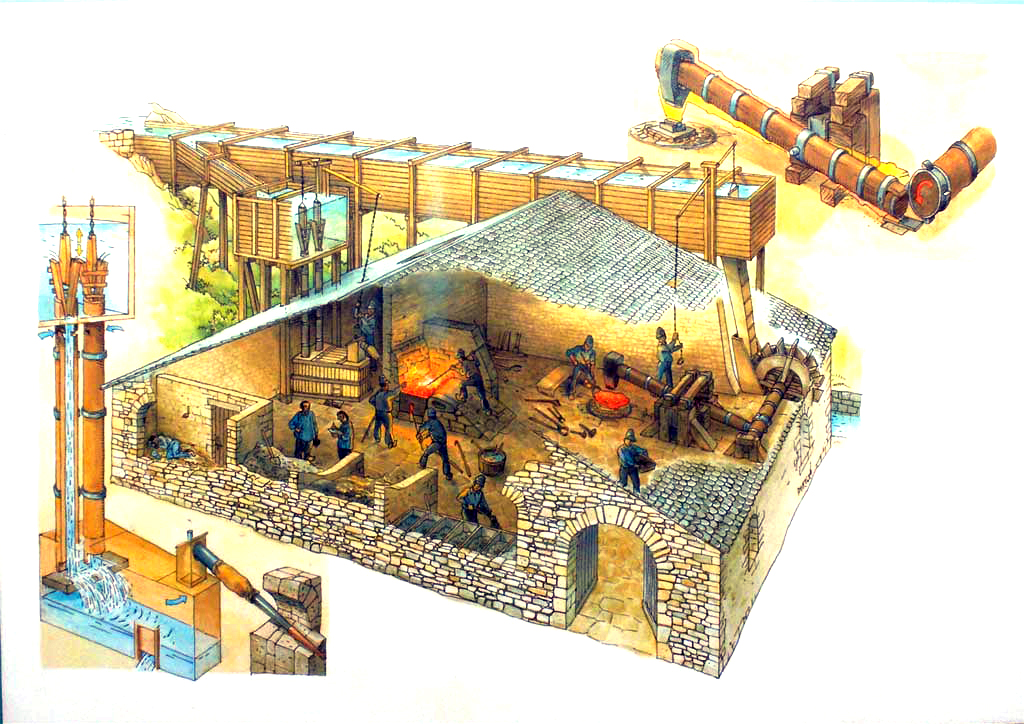
Pertuzé. Forge à la catalane en Pays de Foix
Le bas fourneau
Le bas-fourneau est le cœur de la forge. Il est de petite dimensions (environ 54 cm de long et de large et 43 cm de profondeur). Le fond du creuset, la sole, est en pierre, la face du fond, la rustine, en maçonnerie liée à l’argile, les autres faces sont doublées avec des prismes de fer de 2 quintaux. On laisse un vide, le trou de chio, bouché par de l’argile sur la face de devant pour permettre, au moment voulu, l’écoulement des scories sur le sol de la forge. Les angles sont arrondis avec de l’argile. Le creuset est reconstruit tous les 3 ou 4 mois.
Les trompes
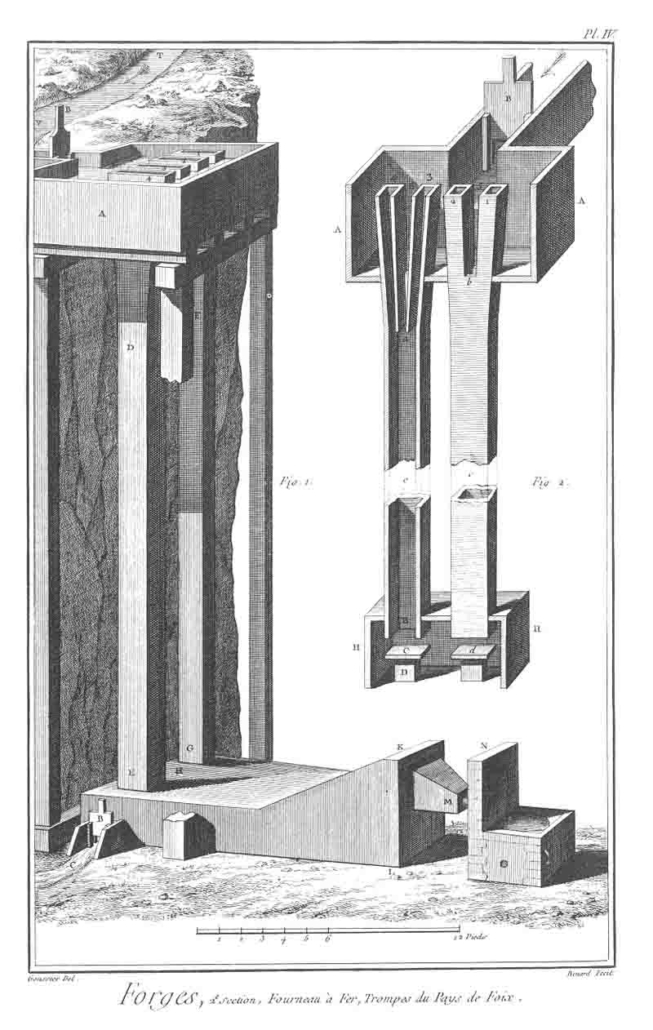
Trompes du Pays de Foix. (Encyclopédie, Forges ou art du fer, deuxième section, planche IV)
Introduites en vallée de l’Ouzom vers 1663, elles remplacent avantageusement les barquis ou soufflets car elles ne comportent pas de pièces en mouvement : l’eau qui s’engouffre dans deux arbres creux percés d’évents ou munis de trompils entraîne l’air. Récupéré dans la “caisse à vent”, l’air est envoyé dans le creuset par l’intermédiaire d’une tuyère en cuivre. Voir le texte accompagnant la planche.
Voir le texte accompagnant la planche[1].
Le Mail et son enclume
À l’origine, le mail est en fer, fabriqué sur place et pèse de 5 à 6 quintaux (200 à 240 kg). Les queues de mail sont en hêtre vert ou en noyer.
Au XIXe siècle, il est en fonte, pèse de 16 à 18 quintaux (650 à 740 kg).
En 1836, on change le marteau de la forge de Nogarot : il est commandé à la fonderie Olim-Chatelet de Toulouse et pèse 695 kg.
L’enclume sur laquelle frappe le mail est au ras du sol, en fer, pèse deux quintaux (82 kg). Elle est enchâssée dans une pièce de fonte, la dame, de 200 à 300 kg. La dame est sertie dans un billot de bois de 1,20 m de diamètre et de 1,20 m de haut qui repose sur un bloc de pierre de 3 à 4 m3 (6 à 8 tonnes).
La roue qui actionne le mail est en bois et mesure 3 m de diamètre. Tout est assemblé par tenons, mortaises et coins. La chute d’eau a 5 à 6 m de haut. L’arbre de la roue mesure 80 cm de diamètre et 6 m de long. Il pèse une tonne.
En 1846, il faut deux jours et 8 paires de boeufs pour conduire un tronc de noyer de Bruges à Nogarot. La réfection de la roue demande 37 journées de travail aux charpentiers attitrés des Angosse : Hourna père et fils, d’Arthez-d’Asson.
L’image mise en avant
Jean-Claude PERTUZÉ (1949-2020) a offert à l’association Fer et Savoir-Faire cette belle illustration d’une forge à la catalane, telle qu’elle était au XIXe siècle.
Jean-Claude Pertuzé était un illustrateur connu.
- Jean-Claude Pertuzé sur Wikipedia
- La liste de tous ses albums sur le site BDovore
Voir aussi
- Tom Richard Études sur l’art d’extraire immédiatement le fer de ses minerais sans convertir le métal en font
- Les forgeurs ariégeois
- Jean Cantelaube et Olivier Codina. La réduction directe et l’acier : le cas à la Catalane (xviie-xixe siècle)
[1] Encyclopédie ou dictionnaire raisonné des sciences, des arts et des métiers, éditée de 1751 à 1772 sous la direction de Diderot et D’Alembert. Forges ou art du fer, seconde section, planche IV.
Mise à jour le 12 mai 2023. 11 janvier 2008 par Émile Pujolle.